Junkei Baseball Gloves
Headquarters: Japan
Year founded: 1946
About Junkei Glove
In 1946, when the Japanese professional baseball pennant race was resumed after the war, “Yoshida Juntageten” raised its voice. The name of the craftsman who became the foundation of Junka Yoshida, JUNKEI-GLOVE is the brand name and company name of the glove as it is, and the aspiration continues to live as a “consecutive soul” for three generations .
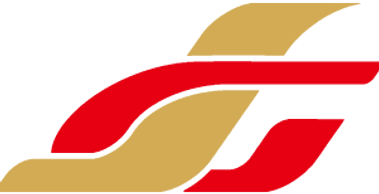
In the first generation , baseball gloves have been produced since the beginning of business. At that time, it was not a time when grabs could be fully produced all year round, but in the 1960s the US, in short the trade as baseball glove production began, and Yoshida Junkei store also supplied many grabs. In the 1970s, grabs by domestic brands were also intensified, and production and supply of grabs as an OEM began. However, after that, production sources of each brand began to switch to cheap overseas production. In the case of overseas production, employees who do not know baseball well do the work of assembling them just as they are said to grab. It is a glove that people who have not played baseball are assembled by mechanical flow work. There is no connection between baseball and sports. A mere assembly plant. If there are 10 workers, 10 different grabs will be produced. While many domestic manufacturers have moved production bases overseas, our grabs have been supported by many players and have continued to be supplied as few domestic production grabs.
What remains unchanged now and then with JUNKEI-GLOVE’s grab is that the same craftsman consistently makes the grab from start to finish. And from the first generation to the second generation, to the third generation production technology, grab type, sewing, inheriting all of the making of the glove, such as typed. This is very important, and it is very important to the stability and quality of the shape of the grab. The disadvantage of overseas production is not just limited to overseas. Whether it is domestic production or an excellent craftsman, regardless of the same brand, different craftsmen make different grabs. There is actually such a funny story. Even today, products manufactured overseas are belt conveyor type and full division of labor. For some workers, you may not be making gloves, but you may only be aware that you are simply processing leather.
A craftsman consistently produces one grab. And that technology will be passed on to the next generation over the years. It will not go overnight in the morning to produce the same grab with the same quality. In the same studio, you can keep making grabs together for decades, and finally make grabs of the same type and quality. This is JUNKEI-GLOVE quality (consecutive soul). And not just making grabs, but supplying many grabs to pro-am players, we will develop better grabs. I think that the number of types of JUNKEI-GLOVE is probably quite large in the industry. It is a grab type that has been developed in many samplings such as player position, play style and handedness. It is no exaggeration to say that we have developed with the players. Craftsman’s arm, and grab type. Of course, it will be stabilized, and it will evolve from year to year. We have also independently designed machines and tools for making grabs. The leather itself also chooses what seems to be the best for a baseball glove. In the history of making gloves over 70 years, JUNKEI-GLOVE is always evolving while inheriting the tradition of orderly soul.
JUNKEI-GLOVE not only manufactures grabs, but many requests for repairs. Among them, the three main types are “frayed and torn leather”, “broken string” and “fray of yarn”. With regard to “fraying and tearing of leather” and “broken rope”, the life can be extended to some extent by leather maintenance and catching technology, etc., but only “fraying of yarn” can not provide effective measures and advice. was. Because the cause of “fraying” is because the “bond yarn” inside the glove is broken by the impact at the time of ball catching. However, after years of research, we have developed products as solutions and solutions for “fraying”. That is the “aramid model”.